In our last blog on this site at Storforth Lane we looked at the history of the Wingerworth and Broad Oaks ironworks, with their blast furnaces, on Storforth Lane. In this blog we bring the story up-to-date.
In 1931 Tarmac acquired the site of Broad Oaks blast furnaces, which had closed in 1907, presumably with a view to recovering slag for use as road metal.
After the Second World War the site passed to Henry Boot, a firm of Sheffield building contractors, who in 1956 established Reema-Boot Ltd. They produced prefabricated concrete sections for both domestic and commercial buildings. Locally this included the mission church at Boythorpe erected by SS Augustine (now the St Francis Community Centre).
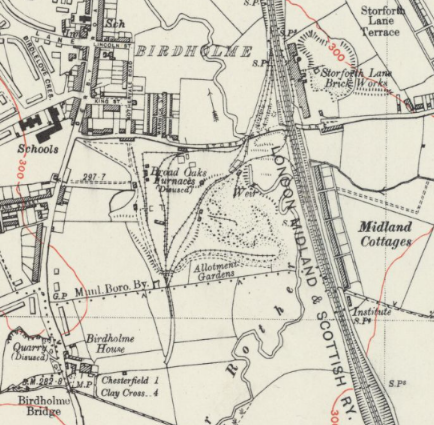
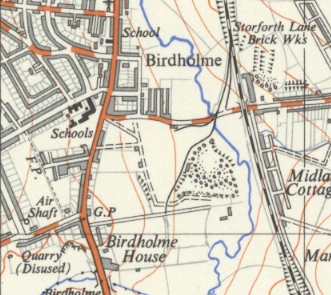
The process was developed by a Wiltshire company, Reed & Mallik (hence Reema) established in 1937. In 1963 it was said that nationally 13,000 Reema houses had been erected, divided between over 400 contracts.
The system involved casting panels the height of a single storey at the works, which could be erected on a prepared foundation with minimal use of skilled labour. The panels slotted into a reinforced concrete frame which tied the building together and ensured that joints between panels were watertight. This method could be used for buildings of up to four storeys, in which load was borne by the frame. For taller buildings the hollow wall panels were filled to provide load-bearing cross-walls. The external wall panels were cast with cavities containing half-inch thick fibreboard insulation. The floor panels were generally hollow. A final external finish to the wall panels was applied at the factory, using various materials, of which gravel proved to amongst the cheapest and most successful. In 1963 it was reported that Reema had been using a range of self-cleaning finishes in glass and china, and some experimental panels had been faced with crushed whisky bottles.
The Storforth Lane factory then had 140 workers, of whom only six were skilled – the joiners who made the wooden moulds for the panels. The factory was using a thousand different moulds, a number which the company pointed out could be reduced to 50 if local authorities would agree on standard designs for houses.
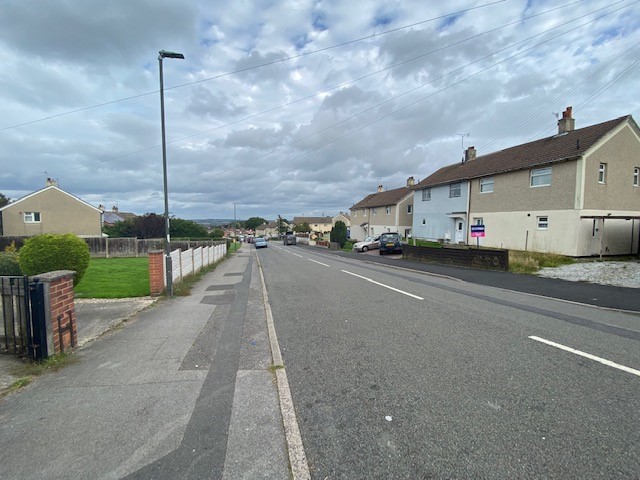
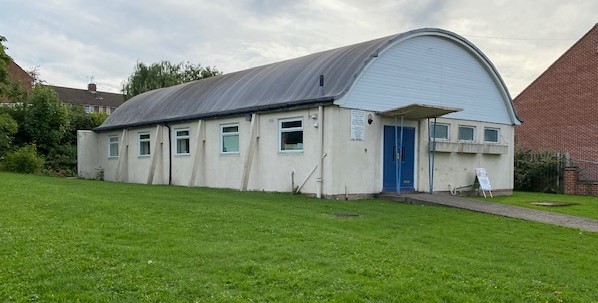
A contract for 2,000 houses for the Coal Industry Housing Association had been produced using only 34 moulds and two types of house. Other differences included the finish required for floors, including timber, thermoplastic, composition, granite or terrazo. Local authorities in the south preferred metal window frames, those in the north timber. In some case heating was ducted, in others embedded.
The company estimated that a factory capable of producing 500 houses a year could be built for £150,000. It had by 1963 built (or had under construction) 2,780 houses at Leeds (Yorks. WR) and between October 1959 and March 1962 had erected 1,810 dwellings.
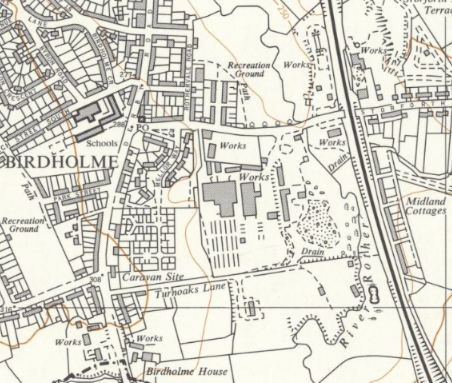
The company was renamed Reema (Chesterfield) Ltd in 1959, in 1975 it became Storforth Contractors Ltd, and in 1976 was dissolved.
After the works went out of use the main ironworks site south of Storforth Lane was redeveloped as an industrial estate, as it still is today.
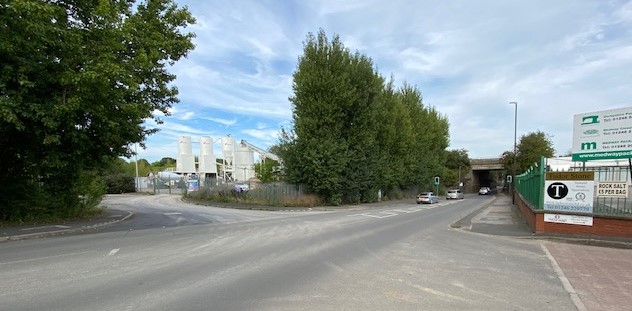
A small area north of Storforth Lane immediately west of the Midland Railway bridge, originally occupied by transfer sidings for the ironworks, continues to be used by a ready-mixed concrete company.
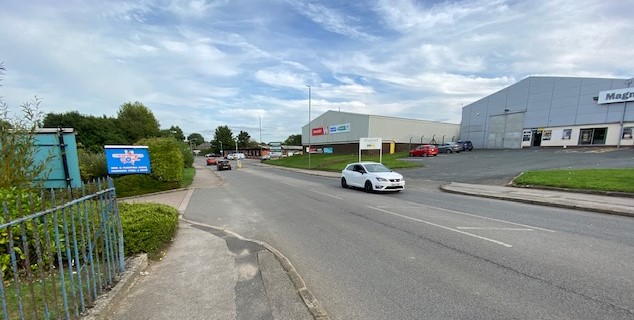
Our Hasland book contains full source references for this blog.
You can learn more about other properties in Hasland in our book – ‘A history of Hasland including Birdholme, Boythrope, Corbriggs, Grassmoor, Hady, Spital and Winsick’. It’s on sale at the Chesterfield Visitor Centre and Waterstones in Chesterfield, priced at £20 for 206 pages with illustrations.
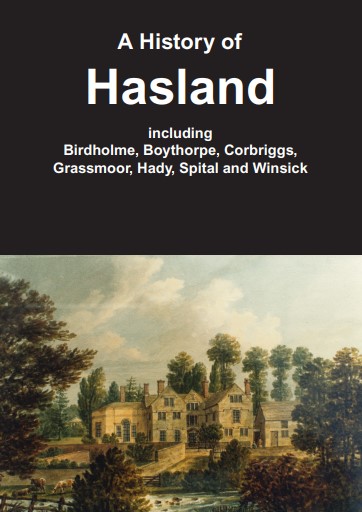